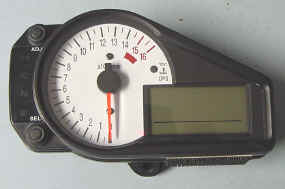
Hopefully this will answer any questions you may have about
changing the backlighting colors of your gauge cluster. You can follow these exact instructions to do this on any
of the following gauges. Others bikes will be very similar but not exactly the same.
-
2000-2003 GSX-R 750
-
2001-2003 GSX-R 600
-
2001-2002 GSX-R 1000.
Tools Needed:
Procedure: Approximate time: 1-2 hours from start to finish
Step 1: Remove the gauge cluster from your
bike by removing the one screw near the bottom center of the gauges. Then pull
the cluster out of it's rubber shock mounts. (Pull straight towards your chest
if you are sitting on the bike.) It may be snug but it will come out. Next,
depress the locking tab on the wiring harness connector on the back and
disconnect the wiring harness.
Step 2: Open the case by removing the 5
screws on the back of the case.
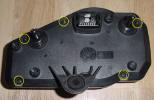
Step 3: Lift the circuit
board out of the case. Carefully lift and remove the needle out of the gauges.
It may be tough but it will come out. Try not to pry with a screwdriver as this
may cause the needle to break. I usually give the needle a counter clockwise
twist as I am pulling it out with my fingers. You may want to try 2 spoons to
pry the needle out. (If you are replacing the white
face, remove the 2 screws immediately above and below the needle.)
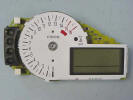
Step 4: Remove 3 screws
holding the front lens onto the circuit board
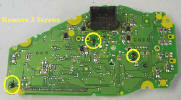
Step 5: De-solder the 30
pins across the bottom. This is necessary to be able to remove the clear lens so
that you can access the LED's. Solder wick is required.
A de-soldering station is highly recommended.
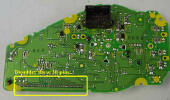
Step 6: Lift clear lens from
circuit board
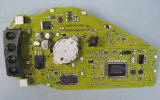
Step 7: Remove the old
LED's. This is probably the hardest part. If you have a tweezer iron, that would
be the best to use. If you only have a regular iron, try to heat one side and
lift it slightly to separate it from the board. Then go to the other side of the
LED and it should come off. If not, go back to the first side and start again.
Do not apply excessive heat. Solder wick is highly recommended. The wick can
pull away excess solder making it easier to separate from the board and it will
also clean the solder from the board making it easier to install the new LED's.
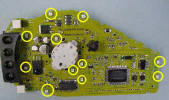
Step 7: Install your new
LED's. You will need 11 LED's. (We would like to share the part numbers we use but we can't give away all of
our secrets ) When installing your new LED's, orientation is
important. On the board near each LED you will see an "A" and "K". The "A"
represents the anode side (+) and the "K" represents the cathode side (-). You
then determine which way the LED must be installed by looking for a mark on the LED
itself. Usually LED's have the cathode marked but be sure to check the
specifications to be sure.
TIP: Use a red LED for the redline to make the redline more visible.
Step 8: Double check all LED
orientations and each solder connection. Do not use too much solder that may
short out with other components. Also make sure there is enough solder that the
connection is solid and won't crack under vibration. It would be best to inspect all joints with a magnifying glass
if you have one.
Step 9: Re-insert clear
plastic lens with 30 pins and fasten with the 3 screws from the back. Make sure
all the leads are through the board and not bent in any way. If you install the
screws first, you can be sure the 30 pins will be inserted all the way and will
not be placed under stress from tightening the screws later if they were
soldered in place already.
Step 10: Solder 30 pins to
the circuit board. As stated before, do not use too much solder that might cause a short
between pins and be sure to use enough so that the joint will not crack under
vibration. Again, inspect all joints with a magnifying glass if possible.
Step 11: Re-install the
needle (and 2 screws for the new faceplate if you are changing it at the same
time.) Simply press the needle back into the hole.
Step 12: Zero out the needle
by turning needle gently counter clockwise until you feel resistance. (Be sure
not to hold the needle in as this will allow it to spin freely all the way
around.) Then continue until the needle is at the zero position.
Step 13: Re-install PCB into
case and attach back panel with 5 screws removed earlier.
Step 14: Reconnect wiring
harness and put back onto your bike. If all goes well, it should then look like
this:
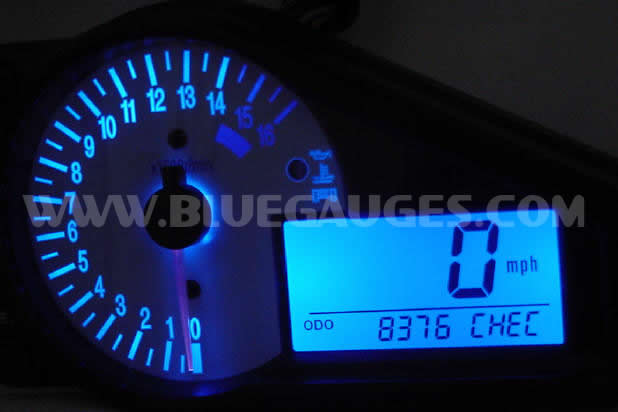
Remember, if it is too much
for you to handle, we can do them for you. Our prices include insured return shipping
within the USA and a lifetime warranty for as long as you own the vehicle
We also have other colors available.
See backlighting service page here.
|